- E7018 is a shielded metal arc welding (SMAW) electrode. 'E' stands for electrode. '70' stands for 70000 psi minimum as welded tensile strength. '1' designates the position the electrode can be.
- Hundreds, if not thousands, of stick electrodes exist, but the most popular fall into the American Welding Society (AWS) A5.1 Specification for Carbon Steel Electrodes for Shielded Metal Arc Welding. These include the E6010, E6011, E6012, E6013, E7014, E7024 and E7018 electrodes. What do AWS stick electrode classifications mean?
AWS A5.1/A5.1M is the Specification for Carbon Steel Electrodes for Shielded Metal Arc Welding: E7018 is one of the most common used stick electrodes rods so it will be used as an example. E7018 E = Electrode, The first two digits = tensile strength minimum in ksi of the weld metal 70,000 psi in this case. E7018-A1 DATA SHEET Pinnacle Alloys E7018-A1 AWS CLASS E7018-A1 H4R CODE AND SPECIFICATION DATA: AWS A5.5 ASME SFA 5.5; UNS W17018 DESCRIPTION: Pinnacle Alloys E7018-A1 electrodes are similar to E7018 carbon steel electrodes classified in AWS A5.1/A5.1M, except that 0.5% molybdenum has been added. This addition increases the. Almost every set of plans I see requires E70XX or E7018 electrodes. But just because your undergraduate steel design textbook used E70XX electrodes in the design example does not mean that is all there is to welding with 70-ksi electrodes. Designers seem to intend 'E70XX' to generically mean 'filler metal with a minimum tensile strength of 70 ksi'.
E7018 Welding Electrode is an outstanding quality all position welding electrode, covered with extra low hydrogen potassium type, coating for welding high tensile steels and low alloy steels. Its nominal welding efficiency is about 110% due to iron powder is contained. The weld metal shows an excellent low temperature toughness and high crack resistance. Ti is widely used in important projects of ships, boilers, high press vessel, bridges, skyscrapers, offshore drilling platforms, nuclear power stations ect. The groove of base metal should be cleared away impurities, and the electrode must be baked at a temperature to 400 degree, then be held 1-2 hours before welding, 2.5mm one should be done by 350 degree, then be held 1 hour.
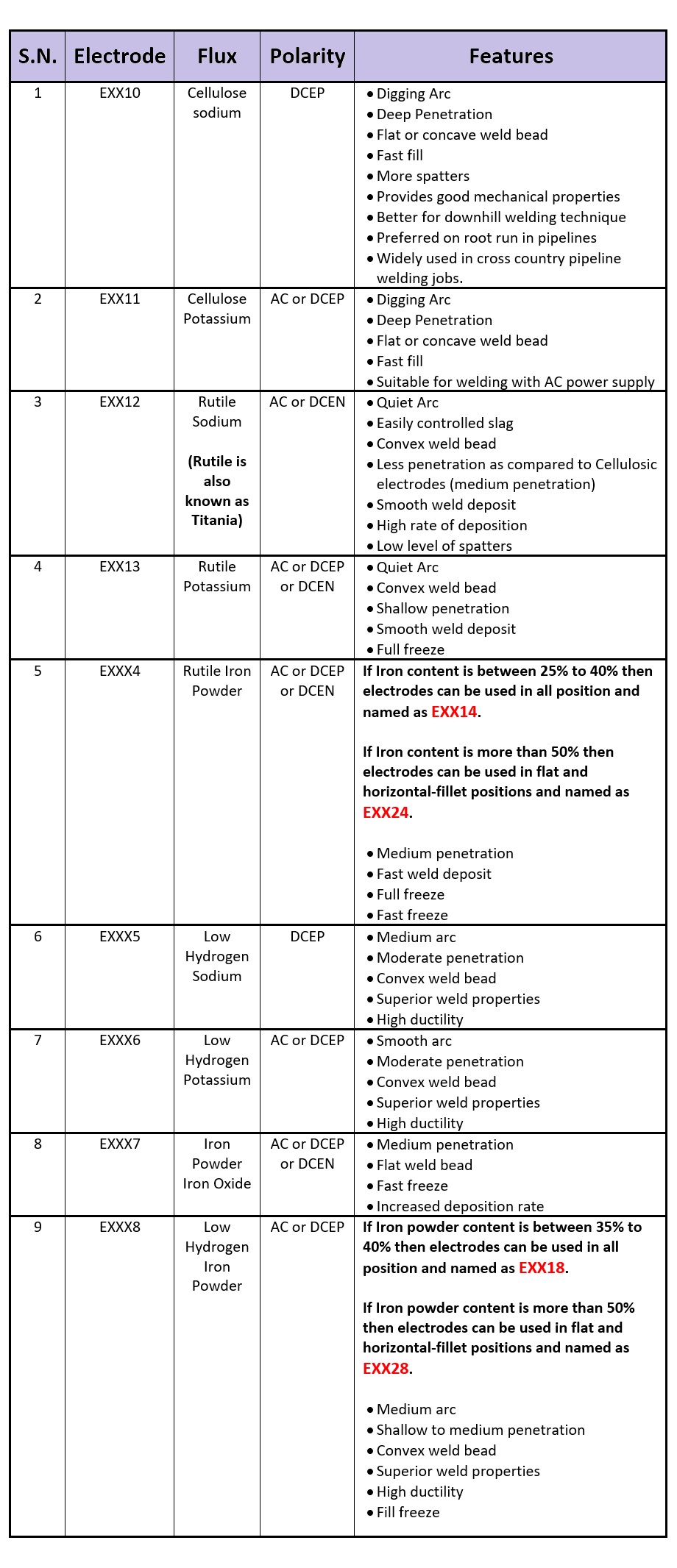

The normal sizes: 2.5*300mm, 3.2*350mm, 4.0*400mm, 5.0*450mm.
Chemical Composition of Deposited Metal (%):
C | Mn | Si | S | P | Cr | Ni | Mo | V | |
Standard | ≤0.15 | ≤1.60 | ≤0.75 | ≤0.035 | ≤0.040 | ≤0.20 | ≤0.30 | ≤0.30 | ≤0.08 |
Typical | 0.068 | 1.36 | 0.51 | 0.010 | 0.016 | 0.047 | 0.022 | 0.010 | 0.014 |
Mechanical Properties of Deposited Metal (%)
Yield Point ReH (Mpa) | Tensile Strength Rm (Mpa) | Elongation A 5 (%) | -20℃(J) | -29℃(J) | -46℃(J) | |
Standard | ≥375 | 490-660 | ≥22 | ≥47 | ≥27 | ≥27 |
Gypical | 440 | 540 | 30 | 170 | 150 | 130 |

Welding Electrode E7018 Meaning Definitions
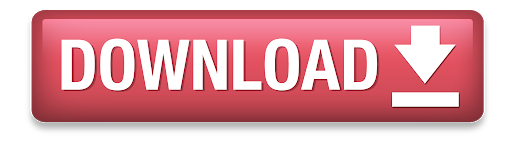